USING THE BEST TOOL
HVAC system comparison tool
Are you involved in the building process and need to make informed decisions about HVAC systems? Whether you're a prospective building owner, an HVAC system design engineer, an architect, or a mechanical contractor, our tool is designed for you.
Over the last 50 years the HVAC System design and bid infrastructure in North America has evolved to enhance the bid process and offer choices for building owners. The Hydronic Industry Alliance has come together to create a resource to assist owners and their design teams in blending the multitude of component choices into complete hydronic systems that support the Integrated Design Process.
Sample output from BEST Software tool (click to enlarge)
Introduction
There is more to total building energy use than just HVAC: The goal of this site is to assist the design team in the early evaluation of “Choices” to integrate the building energy profile into a total HVAC solution.
General Challenges
Energy is currently distributed throughout a building by Water, by Air, and by refrigerant. Refrigerant is best applied in factory-sealed circuits to take advantage of pressure and phase change. It is this circuit that is at the core of mechanical efficiency and requires certification as the basis of energy efficiency. Field construction of refrigerant piping results in the requirement for one supplier’s complex controls and the application of multiple correction factors as built to determine applied performance. Maintenance and safety concerns for refrigerant at 460psi demand factory-sealed circuits or minimal use of pre-charged factory refrigerant lines similar to use in homes.
Field applied transport of energy for competitive bidding, universal design, operation and control uses both water and air as best applied to a unique building per the owners requirements.
- Main energy movement horsepower is lowest in water or pipe which uses approximately 10-15% of that required in ductwork.
- Ventilation air and air movement in the occupied space requires duct work, less efficient but more practical in application for distribution and sound control.
- Terminal solutions depend on space function and energy use versus the budget.
Central Hydronic system vs. distributed vs. hybrid: fundamental choice
- Central – Example: Boilers and Chillers and Pumps
- Lower installed capacity versus terminal system
- Fewer connection points
- Isolate equipment from occupants for sound and service
- Typically longer life equipment
- Distributed Central Systems: Radiant, Chilled Beam, Fan Coil, and /or Water Source Heat Pumps with central system boiler, chiller or fluid cooler with the option for GeoExchange, solar or other Green technology available today or in the future.
- Recommended for high people or plug loads
- Highly variable loads per zone, individualized control or metering
- Isolate perimeter of building from interior
- Hydronic equipment provides for longer system life cycle
- Terminal Air – Rooftop, PTAC, Multi-split, VRF
-
- Terminal Air systems have high total installed capacity
- Low efficiency because air-cooled, medium efficiency and life when water-cooled
- Loss of ability to recycle energy within entire building
- Cannot incorporate water heating and HVAC to recycle cooling to heating
Energy Saving steps – General Guidelines
(Note: Many of the points to follow are included in a series of “Advanced Energy Design Guides” available online and developed in collaboration by: ASHRAE, AIA, IESNA, USGBC, USDOE).
Separate non-typical loads (heating, cooling, filtration, humidity, Air Quality) from each other:
- Ventilation air should be demand controlled based on requirement typically of occupants. Ventilation air is treated one time for temperature, quality, and building pressurization then exhausted. Dedicated Outdoor Air Systems serve this purpose. By treating the outdoor air as required the effect is to reduce the load on the interior, i.e. sensible loads.
- The application of hydronic terminals provides for the treatment of locally generated latent loads (humidity). Dedicated units ensure proper comfort choice, air movement, local air filtration, or reheat. An energy goal would be that any reheat required for a high humidity space would be free heat.
- High load rooms like classrooms, conference, or data and A/V rooms need dedicated treatment. They are also constant sources of heat to be used for perimeter heating, unoccupied heating, and water heating.
- Individual control or metering of energy use: Offices, Retail, Multifamily, assisted living, hotel, dormitory where individual comfort choice is required.
- Highly variable usage or loads
- Perimeter versus interior zones – not only for comfort but thermal isolation of interior when unoccupied to reduce energy consumption.
- Central Chiller efficiency options are multiple. Generally water-cooled chillers are more efficient than air-cooled. The next strategy is staged, stepped or variable capacity to respond to changing load profile in the actual building while taking advantage of diversity. The central chiller is sized for the worst case concurrent loads, but operates efficiently by responding to the actual building load in total. Water-cooled chillers are the most efficient because the compressor functions against water temperatures controlled by the operator versus outside air. The hydronic circuit maintains efficiency and life, while reducing the energy bill as operation is maintained constant even with temperature extremes.
- Cooling towers or Fluid Coolers today use less horsepower, less water and with control options become economizers. The technology is now more than ever adaptable to central green technologies including hybrid GeoExchange.
- Central boiler efficiency has improved dramatically over the last decade and the options in performance capabilities have expanded. For example Boiler efficiency has improve up to 20% plus, and the temperature ranges to respond to radiant applications result in increased efficiency and equipment life.
- Central Pumps are typically applied with Variable Frequency drives today. The selection programs available ensure correct sizing of the main pumps. There are multiple selection tools available from members including option piping schematic systems to reduce energy use and simplify maintenance and control.
- Pipe material choice and system designs are reducing system pressure losses and making the operation of the systems fool proof and easily understood. Pipe options still include Iron and copper, but a multitude of composite options reduce installed cost, chemical use, and flexibility resulting not only in improved HVAC distribution but water heating for both domestic and service requirements. The opportunity to recycle energy from the air conditioning equipment cooling load is enhanced by having both systems in pipe.
- Identify efficiency options and apply to the system as a whole. Avoid the use of or at least be aware of “adjusted” efficiency ratings on equipment. Residential equipment typically uses an SEER or an IEER, they are S for seasonally adjusted, or I for Integrated Energy Efficiency Ratios which means they already have been corrected for weather and part load conditions, which is why the Department of Energy and AHRI (Air Conditioning, Heating, and Refrigeration Institute) publish an EER which is the capacity of the unit divided by its energy consumption. The design team then applies factors based of your building. The Energy Analysis tool on this site provides a top level system evaluations complete with defaults and the ability to change input prior to investing in specific analysis for your building.
- Control Strategy is highly variable based on the building but should consider the following requirements: Central versus individual, occupancy, set-back, optimization of performance, sequencing, economizers, and comfort monitoring. Comfort monitoring is an early warning that the equipment in not performing, may be losing efficiency, or may not be operating efficiently, and serves to cause corrective action prior to increased loss of function.
Click to Submit Peer Review Comments
COMPARE SYSTEMS ON THE FLY
The Building Efficiency System Tool™ saves you time by allowing you to compare up to four different HVAC systems configurations on the fly during the design process. The interactive tool eliminates recalculation time for changes to allow you to quickly and easily compare HVAC system operating and life cycle costs at the beginning of a project.
Published test data doesn’t always equal actual performance. The BEST uses Building Energy Efficiency Ratings (BEER), based on actual system performance data, to output fast efficiency comparisons, and uses real cost data from more than 50 HVAC contractors to output accurate cost estimates for early HVAC system comparison.
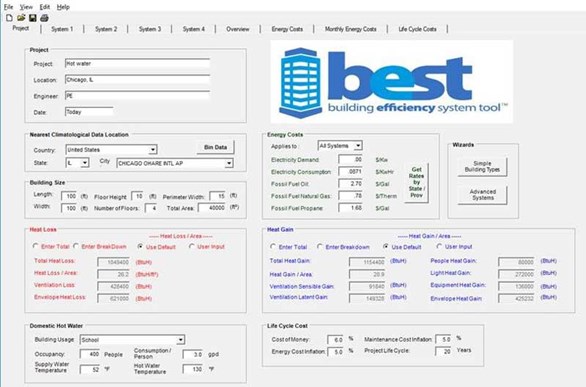
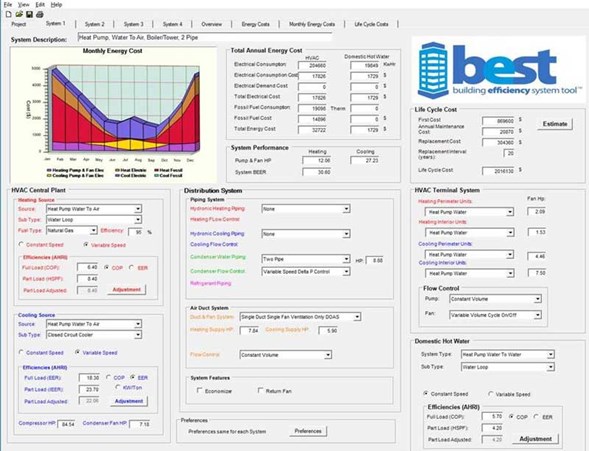
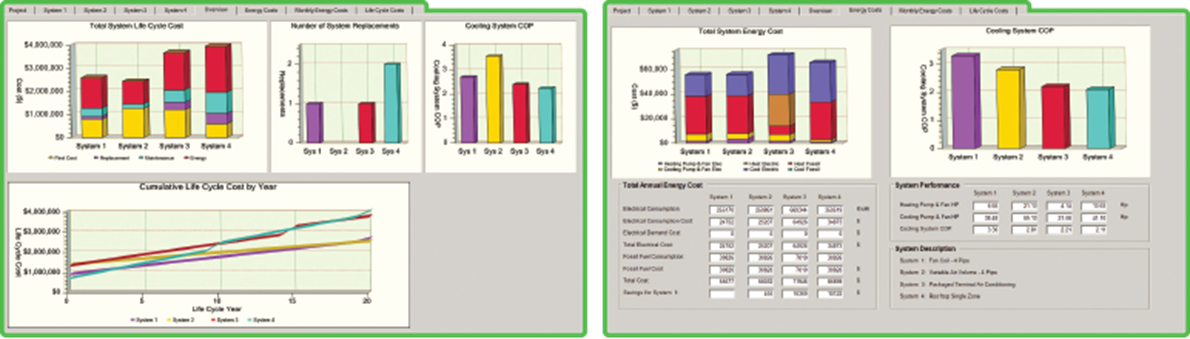